Excellent Industrial Design Student Work: Sapna Tayal's Quilted Furniture
This Quilted Furniture project is by Sapna Tayal, an Industrial Design student at Carnegie-Mellon University. I'd give her an "A;" Tayal has imaginatively harnessed production technology, collaborated with non-ID-department bodies and produced a highly professional level of documentation.Tayal's central question was: "How can we harness the unique capabilities of the overlooked CNC sewing machine, traditionally only used to make soft blankets, and expand its fabrication possibilities?" To get to the answer, she worked with researchers from CMU's Human Computer Interaction Institute (HCII) and Robotics Institute (RI).Flat-to-shape objects fabricated with a CNC sewing machineHow can we harness the unique capabilities of the overlooked CNC sewing machine, traditionally only used to make soft blankets, and expand its fabrication possibilities? Deployable objects allow quick activation and compact storage but often require intricate assembly processes. We establish a novel rapid, scalable method to fabricate functional objects using a large computer-controlled quilting machine (11 ft / 3.4 m wide). Rigid materials like plywood or acrylic are sandwiched between fabric layers and secured through sewing, forming soft hinges. These hinges allow smooth transitions into three-dimensional forms with minimal post-processing. Flat-to-shape steps of the side table Method OverviewLongarm Quilting Machine. Fabric is tensioned over the rollers. Leveraging the machine's strengthsModern CNC quilting machines, offer precision, reliability, and scale. However, their potential remains largely untapped beyond flat, fabric-based products like quilts. We take advantage of the machine's unique features to craft unique, surprising, fully functional objects. Computer-controlled sewing and panel insertion for the backpack design (10x speed).Human-machine co-creation Establishing an incremental fabrication process with alternating passes of sewing pockets and placing inserts.Designed Objects1. Lamp Made up of four panel types for localized functions to achieve dynamic functionality: plain acrylic at the base, cardstock-laminated panels in the inner ring, LED-integrated "active" panels in the upright section, and open spaces at the top for a graceful fabric drape as the lampshade.2. Backpack Inspired by packaging design, a tendon cord system transforms the bag from flat to 3D and doubles as the straps. Made of 3/16" plywood inserts. Gusset panels remain flexible with Velcro for selective attachment and locking.3. Side Table Transforming with a simple tug secured with a spring cord lock while in use. The cord acts on short rectangular struts, which meet in the center under the tabletop when fully deployed, stopping further movement.4. Lounge Chair A large (60" by 56" when flat) chair designed to support an adult's weight.The insert panels, made from 1/2" plywood cut on a CNC router, are designed to meet face-to-face when deployed. Neodymium magnets, glued into milled pockets, allow the chair to "snap" into place, aligning the panels, while the fabric and panels carry the primary loads.Design ProcessSewing PossibilitiesA research-through-design process to play with different sewing and gathering methods and studying their effects. Geometry and Method TuningPrototyping possible forms. Technical ProcessChair fabrication process where a table and weights are used to build objects larger than the bed size.Scaling upWe adapt the machine (11 ft x 25 in sewing area) for large scale rigid panel fabrication by replacing the typical fabric rolling method with a height-adjustable table. A weighted rod threaded through the fabric edge maintains tension and alignment during stitching.Original machine set up: Our modifications to expand fabrication scope: Path and Panel Sequence AlgorithmIn the full research paper, we formalize a repeatable design space to share our discoveries. Reach out for more information! Putting the CNC Sewing machine together! Mid-project we needed to move the machine (~13' by 5') from its original home in Robotics to the HCI lab across campus.Taking the machine apart and putting it back together was an incredible opportunity to learn about its workings and nuances of operating it! You can see more of Tayal's work here.
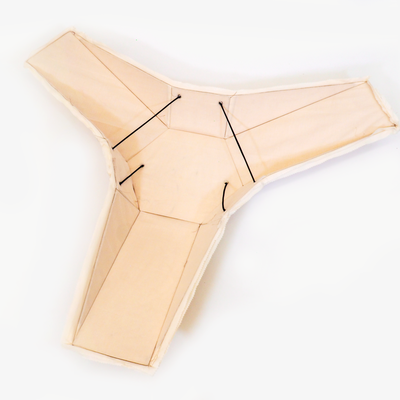
This Quilted Furniture project is by Sapna Tayal, an Industrial Design student at Carnegie-Mellon University. I'd give her an "A;" Tayal has imaginatively harnessed production technology, collaborated with non-ID-department bodies and produced a highly professional level of documentation.
Tayal's central question was: "How can we harness the unique capabilities of the overlooked CNC sewing machine, traditionally only used to make soft blankets, and expand its fabrication possibilities?" To get to the answer, she worked with researchers from CMU's Human Computer Interaction Institute (HCII) and Robotics Institute (RI).
Flat-to-shape objects fabricated with a CNC sewing machine
How can we harness the unique capabilities of the overlooked CNC sewing machine, traditionally only used to make soft blankets, and expand its fabrication possibilities?
Deployable objects allow quick activation and compact storage but often require intricate assembly processes. We establish a novel rapid, scalable method to fabricate functional objects using a large computer-controlled quilting machine (11 ft / 3.4 m wide). Rigid materials like plywood or acrylic are sandwiched between fabric layers and secured through sewing, forming soft hinges. These hinges allow smooth transitions into three-dimensional forms with minimal post-processing.
Flat-to-shape steps of the side table
Method Overview
Longarm Quilting Machine. Fabric is tensioned over the rollers.
Leveraging the machine's strengths
Modern CNC quilting machines, offer precision, reliability, and scale. However, their potential remains largely untapped beyond flat, fabric-based products like quilts.
We take advantage of the machine's unique features to craft unique, surprising, fully functional objects.
Computer-controlled sewing and panel insertion for the backpack design (10x speed).
Human-machine co-creation
Establishing an incremental fabrication process with alternating passes of sewing pockets and placing inserts.
Designed Objects
1. Lamp
Made up of four panel types for localized functions to achieve dynamic functionality: plain acrylic at the base, cardstock-laminated panels in the inner ring, LED-integrated "active" panels in the upright section, and open spaces at the top for a graceful fabric drape as the lampshade.
2. Backpack
Inspired by packaging design, a tendon cord system transforms the bag from flat to 3D and doubles as the straps. Made of 3/16" plywood inserts. Gusset panels remain flexible with Velcro for selective attachment and locking.
3. Side Table
Transforming with a simple tug secured with a spring cord lock while in use. The cord acts on short rectangular struts, which meet in the center under the tabletop when fully deployed, stopping further movement.
4. Lounge Chair
A large (60" by 56" when flat) chair designed to support an adult's weight.
The insert panels, made from 1/2" plywood cut on a CNC router, are designed to meet face-to-face when deployed. Neodymium magnets, glued into milled pockets, allow the chair to "snap" into place, aligning the panels, while the fabric and panels carry the primary loads.
Design Process
Sewing Possibilities
A research-through-design process to play with different sewing and gathering methods and studying their effects.
Geometry and Method Tuning
Prototyping possible forms.
Technical Process
Chair fabrication process where a table and weights are used to build objects larger than the bed size.
Scaling up
We adapt the machine (11 ft x 25 in sewing area) for large scale rigid panel fabrication by replacing the typical fabric rolling method with a height-adjustable table. A weighted rod threaded through the fabric edge maintains tension and alignment during stitching.
Original machine set up:
Our modifications to expand fabrication scope:
Path and Panel Sequence Algorithm
In the full research paper, we formalize a repeatable design space to share our discoveries. Reach out for more information!
Putting the CNC Sewing machine together!
Mid-project we needed to move the machine (~13' by 5') from its original home in Robotics to the HCI lab across campus.
Taking the machine apart and putting it back together was an incredible opportunity to learn about its workings and nuances of operating it!
You can see more of Tayal's work here.