Brake-Formed Furniture by Industrial Designer George Davies
Industrial designer George Davies works primarily with 1/8"-thick sheet metal and a brake. Within these limitations, and inspired by 20th-century designers like Gerrit Reitveld, Charlotte Perriand, Le Corbusier and the Eameses, Davies creates furniture that celebrates his chosen material and production method and leaves the joinery methods transparent."Most of my work revolves around brake forming, which is both the core of my design aesthetic and my biggest technical limitation," Davies said in an interview with Null Society.GD-PC2Brake Formed Patio Chair "The process requires bending sheet metal into precise forms, but it comes with constraints—certain bends aren't possible without material collisions, and sometimes I have to revise designs based on what the press-brake machine can physically handle. It's a frustrating but rewarding challenge, as it forces me to think within a strict set of manufacturing parameters."Untitled commissionBrake Formed Aluminum Buffet Table "What I love most about this process is its incredible precision and repeatability. Unlike traditional prototyping, where I'd build scale models out of wood or foam before committing to a full-scale piece, brake-forming allows me to prototype at full scale from the start. Whatever I design in CAD is exactly what I'll get in person, so I spend a lot of my time dialing everything in on the CAD side. Even my first prototypes tend to be functional at a minimum-viable level, requiring only small refinements instead of major overhauls."GD-SC1Brake Formed Aluminum Slipper Chair "A big part of my design philosophy is embracing raw materiality and manufacturing clarity. I intentionally leave many surfaces untouched, preserving the random printed mill/lot codes, scratches, and, most notably, the brutal witness marks etched into both sides of each bend by the press-brake tooling. These details tell the story of how the piece was made—they aren't flaws, but rather evidence of the industrial process. I love that every bend, cut, and mark reflects the journey from sheet metal to finished form." The full interview is worth a read. Davies discusses form, design details, production details, and tells a story from his ID school days, where he faked his way into the welding studio without yet knowing how to weld.You can see more of Davies' stuff here.
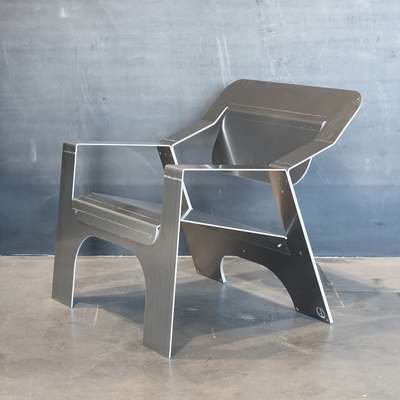
Industrial designer George Davies works primarily with 1/8"-thick sheet metal and a brake. Within these limitations, and inspired by 20th-century designers like Gerrit Reitveld, Charlotte Perriand, Le Corbusier and the Eameses, Davies creates furniture that celebrates his chosen material and production method and leaves the joinery methods transparent.
"Most of my work revolves around brake forming, which is both the core of my design aesthetic and my biggest technical limitation," Davies said in an interview with Null Society.
GD-PC2
Brake Formed Patio Chair
"The process requires bending sheet metal into precise forms, but it comes with constraints—certain bends aren't possible without material collisions, and sometimes I have to revise designs based on what the press-brake machine can physically handle. It's a frustrating but rewarding challenge, as it forces me to think within a strict set of manufacturing parameters."
Untitled commission
Brake Formed Aluminum Buffet Table
"What I love most about this process is its incredible precision and repeatability. Unlike traditional prototyping, where I'd build scale models out of wood or foam before committing to a full-scale piece, brake-forming allows me to prototype at full scale from the start. Whatever I design in CAD is exactly what I'll get in person, so I spend a lot of my time dialing everything in on the CAD side. Even my first prototypes tend to be functional at a minimum-viable level, requiring only small refinements instead of major overhauls."
GD-SC1
Brake Formed Aluminum Slipper Chair
"A big part of my design philosophy is embracing raw materiality and manufacturing clarity. I intentionally leave many surfaces untouched, preserving the random printed mill/lot codes, scratches, and, most notably, the brutal witness marks etched into both sides of each bend by the press-brake tooling. These details tell the story of how the piece was made—they aren't flaws, but rather evidence of the industrial process. I love that every bend, cut, and mark reflects the journey from sheet metal to finished form."
The full interview is worth a read. Davies discusses form, design details, production details, and tells a story from his ID school days, where he faked his way into the welding studio without yet knowing how to weld.
You can see more of Davies' stuff here.