3 Ways Designers Can Incorporate Sustainable Workflows
In today's competitive consumer products industry, incorporating sustainability considerations into the product design process is not just a buzzword but a necessity. However, for many design firms, achieving sustainable outcomes can feel daunting and unachievable due to preconceived notions of cost or what sustainability "should" look like during the design process. Selecting more sustainable materials tends to be the first path forward that springs to mind, but that’s not the only way to integrate sustainable practices into the product design process. Today, designers are leveraging digital tools to eliminate paper trails, streamline processes, and more. Here, we highlight three companies that demonstrate sustainability is not only attainable but also actively practiced in various ways by product designers today. Leveraging sustainability analytics for informed decisions R&S Robertson, renowned for delivering exceptional lighting solutions for the hospitality and leisure sectors since 1939, recently decided to branch out and design its first lighting collection with the design firm Vivid Nine. The Vivid Nine team utilized the Manufacturing Sustainability Insights (MSI) add-on for Autodesk Fusion to calculate the environmental impact of their designs in real-time, even before prototyping and manufacturing. By selecting different materials, manufacturing processes, and locations, MSI provides a comprehensive cradle-to-gate analysis of the product's carbon emissions. This real-time feedback allows designers to experiment with various materials and processes, helping them identify the most sustainable options. MSI’s analysis highlighted the biggest carbon contributors in the designs, indicating areas for significant improvements through material choice changes or design optimizations. Additionally, the team could compare the environmental impacts of manufacturing in different locations. They concluded that it was more environmentally beneficial to manufacture in Portugal compared to Asia, aligning with R&S Robertson’s manufacturing partner in Portugal.The Vivid Nine team utilized the MSI add-on for Autodesk Fusion to calculate the environmental impact of their designs in real-time . “We can go through each component piece of the light and run calculations of different CO2 values to try and reduce it,” says Jonathan Pearson, co-founder, Vivid Nine. “We can compare different manufacturing methods or different sizes to reduce the number. You can have a load of parts. But, with MSI, it’s easy to see what stands out as a really high value from a CO2 perspective and focus on what to change and impact the overall value.” Reducing the production paper trail Termobrasa, a Portugal-based manufacturer of heating systems, has eliminated its paper trail by designing its products in Fusion and tracking their production with Fusion Operations. Fusion Operations provides real-time insights into materials, production schedules, and inventory levels, facilitating efficient resource planning. By digitalizing their operations from design to production, Termobrasa has significantly reduced its reliance on paper, thereby cutting down on resources and embracing a more sustainable. Easy repairs to support the circular economy Native Instruments, a leading manufacturer of software and hardware for music production and DJing, offers a repair program for its products. This initiative focuses on extending the lifecycle of their products, thereby reducing electronic waste. “Usually, customers ask us to ship a spare part that they need to repair their own instruments,” says Matthias Geserick, senior customer care agent, Native Instruments. “Fusion Manage enables me to just find it directly in the database and send it to the customer with all the specs they need.”This approach aligns with the principles of a circular economy, where products are designed to be reused, repaired, and recycled, ultimately minimizing environmental impact. By focusing on access to easy repairs or replacement parts, Native Instruments can be more sustainable and keep customers sampling, composing, and mixing on their beloved instruments for years to come.By incorporating sustainable practices into the design process beyond just considering material type, design teams can reduce their environmental impact and enhance their reputation in an increasingly competitive market where consumers expect more from their products and the teams that create them. Learn more about Autodesk Fusion here.
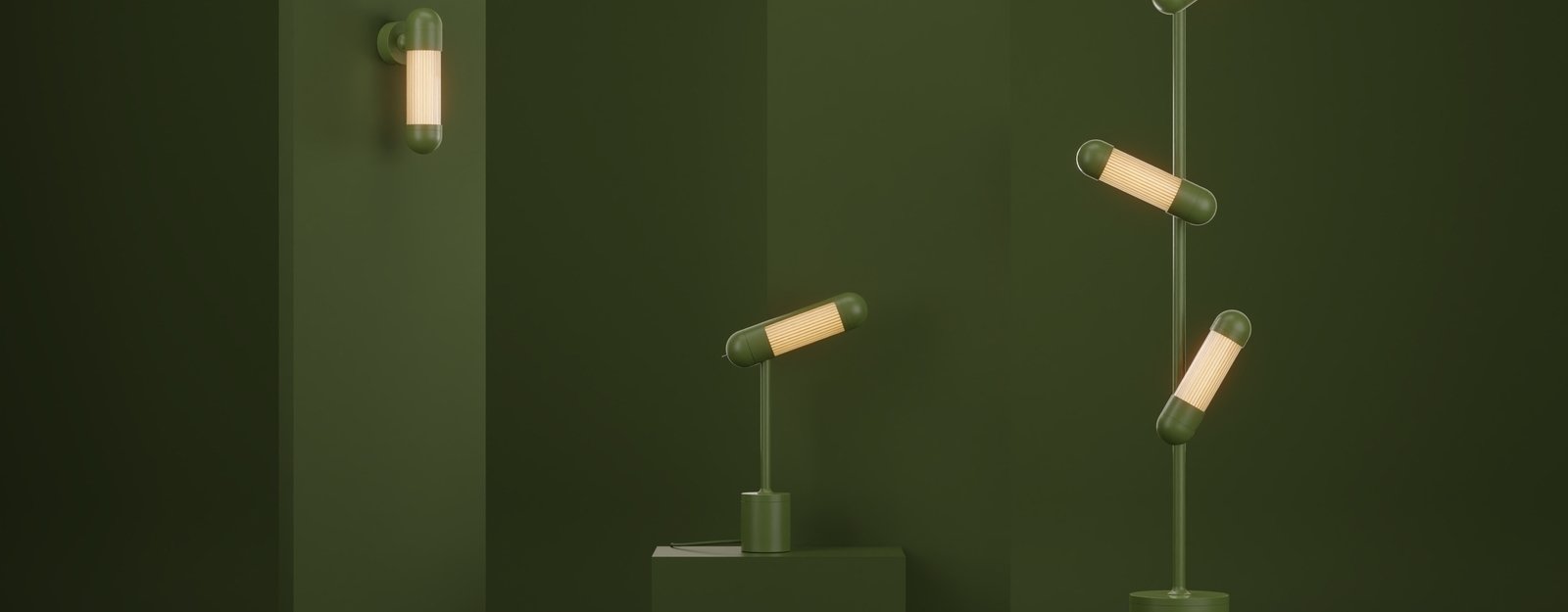
In today's competitive consumer products industry, incorporating sustainability considerations into the product design process is not just a buzzword but a necessity. However, for many design firms, achieving sustainable outcomes can feel daunting and unachievable due to preconceived notions of cost or what sustainability "should" look like during the design process.
Selecting more sustainable materials tends to be the first path forward that springs to mind, but that’s not the only way to integrate sustainable practices into the product design process. Today, designers are leveraging digital tools to eliminate paper trails, streamline processes, and more. Here, we highlight three companies that demonstrate sustainability is not only attainable but also actively practiced in various ways by product designers today.
Leveraging sustainability analytics for informed decisions
R&S Robertson, renowned for delivering exceptional lighting solutions for the hospitality and leisure sectors since 1939, recently decided to branch out and design its first lighting collection with the design firm Vivid Nine.
The Vivid Nine team utilized the Manufacturing Sustainability Insights (MSI) add-on for Autodesk Fusion to calculate the environmental impact of their designs in real-time, even before prototyping and manufacturing. By selecting different materials, manufacturing processes, and locations, MSI provides a comprehensive cradle-to-gate analysis of the product's carbon emissions.
This real-time feedback allows designers to experiment with various materials and processes, helping them identify the most sustainable options. MSI’s analysis highlighted the biggest carbon contributors in the designs, indicating areas for significant improvements through material choice changes or design optimizations. Additionally, the team could compare the environmental impacts of manufacturing in different locations. They concluded that it was more environmentally beneficial to manufacture in Portugal compared to Asia, aligning with R&S Robertson’s manufacturing partner in Portugal.
The Vivid Nine team utilized the MSI add-on for Autodesk Fusion to calculate the environmental impact of their designs in real-time .
“We can go through each component piece of the light and run calculations of different CO2 values to try and reduce it,” says Jonathan Pearson, co-founder, Vivid Nine. “We can compare different manufacturing methods or different sizes to reduce the number. You can have a load of parts. But, with MSI, it’s easy to see what stands out as a really high value from a CO2 perspective and focus on what to change and impact the overall value.”
Reducing the production paper trail
Termobrasa, a Portugal-based manufacturer of heating systems, has eliminated its paper trail by designing its products in Fusion and tracking their production with Fusion Operations. Fusion Operations provides real-time insights into materials, production schedules, and inventory levels, facilitating efficient resource planning. By digitalizing their operations from design to production, Termobrasa has significantly reduced its reliance on paper, thereby cutting down on resources and embracing a more sustainable.
Easy repairs to support the circular economy
Native Instruments, a leading manufacturer of software and hardware for music production and DJing, offers a repair program for its products. This initiative focuses on extending the lifecycle of their products, thereby reducing electronic waste. “Usually, customers ask us to ship a spare part that they need to repair their own instruments,” says Matthias Geserick, senior customer care agent, Native Instruments. “Fusion Manage enables me to just find it directly in the database and send it to the customer with all the specs they need.”
This approach aligns with the principles of a circular economy, where products are designed to be reused, repaired, and recycled, ultimately minimizing environmental impact. By focusing on access to easy repairs or replacement parts, Native Instruments can be more sustainable and keep customers sampling, composing, and mixing on their beloved instruments for years to come.
By incorporating sustainable practices into the design process beyond just considering material type, design teams can reduce their environmental impact and enhance their reputation in an increasingly competitive market where consumers expect more from their products and the teams that create them.
Learn more about Autodesk Fusion here.